Discover EdgeMethods’ suite of solutions designed to drive digital transformation, optimise operations, and unlock value across your business.
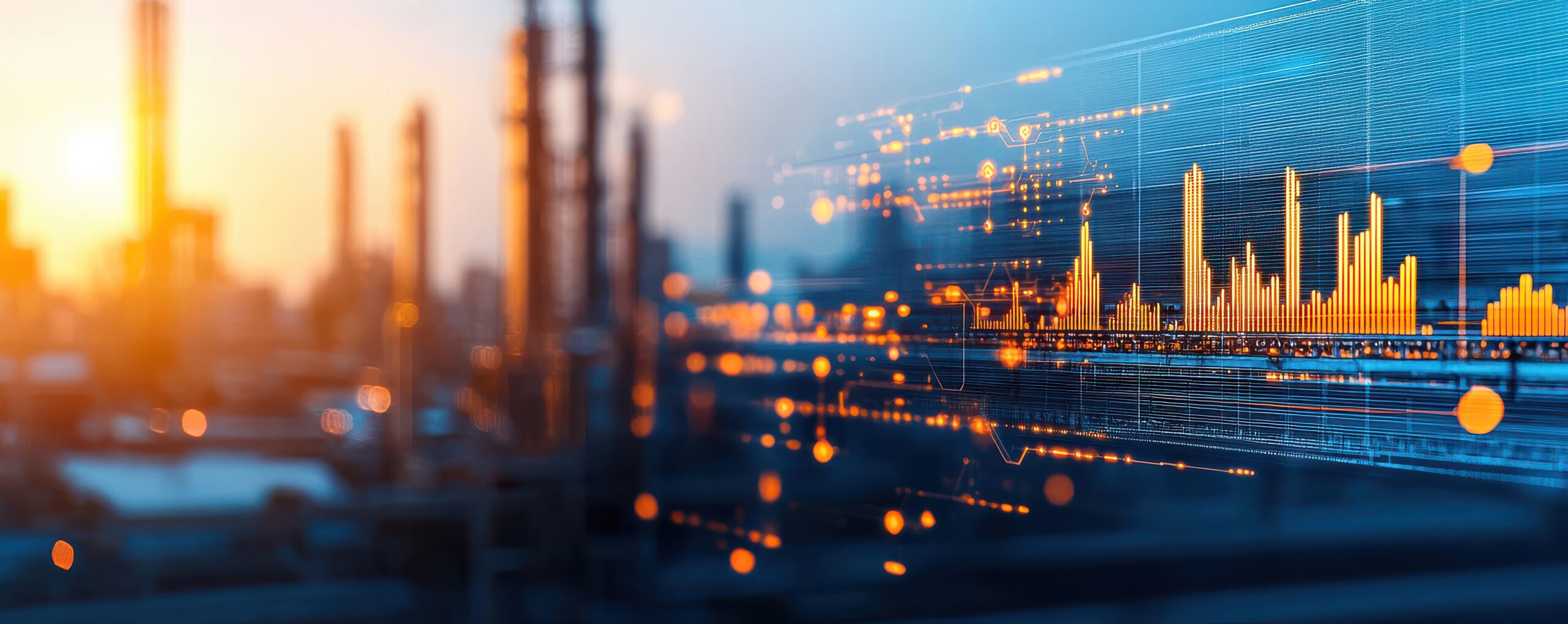
An IoT company has developed a scalable Smart Factory solution leveraging machine learning, digital twins and advanced analytics to drive sustainable growth and operational efficiency.
EdgeMethods, based in High Wycombe, collaborated with Victrex, a Lancashire-based PEEK and PAEK-polymer manufacturer, as part of the Made Smarter Innovation’s Sustainable Smart Factory programme. The project focused on Powder Plant 3 (PP3) at Victrex’s Blackpool site, utilising automated data collection, machine learning algorithms, digital twin technology, advanced analytics, and visualisation tools.
This innovative Smart Factory SaaS solution measures energy consumption, emissions, and costs while enhancing data visibility. It uncovers actionable insights and opportunities in energy efficiency, operational performance, and cost optimisation, equipping Victrex with the tools to drive impactful, data-driven decisions.
The project uncovered previously hidden insights and opportunities for energy efficiency and carbon footprint reduction within PP3. By enhancing data visibility on critical metrics such as high energy consumption, it provides a data-driven foundation for decision-making. This empowers Victrex to target areas like reducing reliance on carbon credits, identifying significant energy usage patterns, and implementing efficiency improvements across the production process. These insights position Victrex to achieve up to 20% energy savings and a 15% reduction in carbon emissions in the future.
EdgeMethods is in advanced discussions with major manufacturers across process industries and has now launched three new SaaS products on the Microsoft Azure Marketplace: EdgeMethods Industry 4.0 Data Platform, EdgeMethods Energy Management and Insights, and EdgeMethods OEE AI.
Chris Needham, Innovation Lead in the Made Smarter Innovation Challenge said:
“To make things greener, we need to make things smarter. This is where digital technologies will be key to the net-zero transition. EdgeMethods and Victrex have demonstrated the staggering insights and gains that can be achieved with a data-led approach to manufacturing.”
The Inspiration
Manufacturing is responsible for 17% of the UK’s greenhouse gas emissions, making decarbonisation one of the industry’s most pressing challenges.
Pressure to adopt sustainable practices is intensifying from all directions -employees, customers, regulators, investors, and local communities. However, measuring emissions, establishing benchmarks, and implementing effective decarbonisation plans is complex, especially when energy usage and reporting standards are often inconsistent or incomplete.
Victrex, as part of its broader ambition to achieve net-zero emissions by 2050, recognised the need to address inefficiencies in energy consumption. The company partnered with EdgeMethods to explore how Industry 4.0 technologies could enhance energy monitoring, provide actionable insights, improve operational efficiency, and uncover opportunities to reduce both costs and environmental impact.
The focus was on Powder Plant 3 (PP3), a critical stage in Victrex’s production stream, where high energy consumption presented a clear opportunity for improvement.
The Innovation
The project focussed on the powder process, the first stage of a complex production stream at Victrex’s Blackpool factory, and what could be achieved by implementing a cutting-edge Energy Management System (EnMS), leveraging IoT technologies, machine learning, digital twin technology, virtual energy meters, advanced analytics and reporting, and novel visualisation tools.
The first stage calculated energy consumption across the plant, processes, assets, sub assets and components. By mapping out the physical metering, EdgeMethods was able to identify the gaps, where energy data was needed.
EdgeMethods then created virtual energy meters, software-based tools that use advanced algorithms and data analytics to estimate energy consumption across assets and processes. This meant Victrex could avoid the immediate need to retrofit additional physical meters, which would be a capital cost and potentially disrupt operations.
Data was then aggregated, cleansed and unified within a central data repository.
The next stage developed a plant and sustainability digital twin. The plant twin was a real-time, accurate digital replica of physical assets and production processes. The sustainability digital twins focussed on analysing energy flows, inferring consumption, and calculating emissions and associated costs.
The final stage was the development of a platform (name?) for advanced analytics and reporting. This enabled real-time monitoring to identify energy inefficiencies instantly and deliver actionable suggestions for immediate operational improvements, and continuous optimisation. The platform also delivers predictive analysis through forecasting future energy usage and suggesting proactive maintenance strategies to prevent inefficiencies and downtime.
Energy Cascade Models compare the ‘theoretical’ energy optimum – what is possible by using cutting-edge technologies, optimal processes and optimal conditions – and the ‘operational’ energy optimum – the existing conditions – to provide clear insights into where energy is consumed and wasted.
Meanwhile, the platform produces energy loss reports for both ‘dynamic’ data, for example, batch by batch, and ‘static’ data, for example, machine degradation, to identify improvement opportunities.
The Impact
The project delivered the following transformative benefits for PP3:
Real-time monitoring and predictive analysis highlighted previously unnoticed inefficiencies in energy consumption, offering valuable insights that enable more effective and impactful decision-making.
Victrex is on track to achieve up to 20% energy savings and a 15% reduction in carbon emissions within Powder Plant 3 (PP3), aligning with its net-zero ambitions.
Improved data visibility has empowered Victrex to make more informed decisions, implement proactive maintenance strategies, and uncover opportunities to reduce costs throughout its operations.
The project has embedded a strong digital transformation culture within Victrex, engaging teams across the company to leverage data-driven tools for continuous improvement and innovation.
Simon Crompton, at Victrex: “The ability to monitor and investigate our production processes near real-time is revolutionary. We are now able to answer questions at speed with the relevant supporting data. We are now believers.”
Stuart Lowe, Co-Founder and Managing Director of EdgeMethods, said: “Our approach has been to create a scalable solution stack which gives a business immediate insights where impact can be derived from and use that core understanding and infrastructure to tackle other areas of the business on a case by case basis. This enables a manufacturer to accelerate their speed to value when reporting emissions internally and externally becomes essential.
“The outcomes of this project have given us the opportunity to start conversations with other process manufacturers of plastics, chemical, pharmaceutical, and food and drink.”
“While the nuances are different from business to business, a lot of the challenges are very similar. Knowing where to start is the hardest point. The level of opportunity is massive.”